I recently encountered a gimbal that had no power, no-LED-indication type dead. The gimbal had been subjected to a fault from Solo’s main board. An odd occurrence, but the following shared knowledge may help someone resurrect a faulty gimbal or assist in trouble shooting other gimbal faults.
First, I am no electronics person and have no background for such things. I am a mechanical piddler, being that I fix and modify things that are mechanical. So I depend heavily on the knowledge of others, the internet and Mouser to plod my way through electronics’ issues. @just_bruce was my guide for trouble shooting this power faulted gimbal, Thank you Bruce.
If you find error with any of the following, please correct me. I’m just conveying my understanding for the component and its place within the given function.
The gimbal has three PCBs, each has CAN and a motor control circuitry for its associated motor. PAN, ROLL and TILT/Pitch. Here is what I understand for these three boards…
PAN-PCB – This board is typically the board to fail. It has the most exposure and the more delicate connectors. It distributes the various power and protection needs to the gimbal from Solo. Hosts the HDMI-FFC connection to the micro HDMI connector. And has a motor control circuitry.
ROLL-PCB – This board is strictly a motor control circuit board. It is somewhat vulnerable to damage or handling type failures. It taps off the power/data ribbon running down the gimbal. This board’s components allowed me to isolate the PAN-PCB’s power/protection circuit from the 8-Pin click-mate connector and then to the Data-FFC.
TILT-PCB – This is the main board of the gimbal, all the brains reside here. It is less likely to be the point of failure as it is well protected by its housing. The IMU, gimbal’s comms, Hero’s comms & port and a motor control circuit reside on this tiny board. It also has attached a potentiometer via ribbon cable to indicate its motor’s position.
HDMI’s ribbon is a homerun from the camera to the HDMI-FFC on the PAN-PCB. If you have video issues, isolated to the gimbal, then you basically have four items to inspect. Primary cause is the micro HDMI connector on the PAN-PCB. Then next would be the HDMI-FFC, ribbon or the HDMI micro that connects to the camera. There is no video conversion done on the gimbal, it all happens in the IMX6.
Data/Power ribbon, terminates to all three PCBs via its respective DATA-FFC, there are two version of this connector. If the ribbon is damaged in any way you are SOL, as there are no replacements unless by salvage. I can’t stress enough to release the ribbons from their FFC before disassembling a gimbal.
Final note regarding disassembly, all three motors have keyed shaft adapters held by grub screws to the keyed motor shafts. Orientation is critical, indicate/mark before disassembly. These adapters have through holes for securing to their respective arm, so orientation can be off by 180⁰ if improperly installed. Also the screw for the arm mount is secured by a grub screw through the end of the exposed adapter. Remove this grub screw first, it requires a 1.3mm hex.
So back to the original story, what I did to fix a dead gimbal. I tested the PAN-PCB board off the gimbal and powered by the J1 connector as normal from Solo.
I was able to isolate a protection/distribution circuit off the PAN-PCB. It appears that U6 & U7 make up that circuit. TP24 was reading about 2.940v, it should have the full battery voltage, 15.16v as an example. I believe the point of failure was between the two chips, not certain if both or one was faulted. I replaced U6 and the voltage tested low again at TP24.
Replacing U7 from a donor board and then TP24 showed the 15.16v. TP21 & TP22 prior was 3.48v and after U7 it was 4.26v. TP23 was zero on all tests, I assume this is the third phase of the BL motor.
I reassembled the repaired PAN-PCB to the gimbal and installed onto Solo. Initially the gimbal powered up with a green LED and then it turned orange indicating a reset or calibration. Once done it returned to green and I had full auto and manual control of the gimbal. It was stable in both low and high torque modes…success.
Here are the list of components that I’ve ID’d over the last few years. I have little ability to ID the traces through the boards, identifying what is what. Would be nice to have a schematic! Again trial and error, voltage and a continuity meter to hack through it all. As to resistors and capacitor, those will likely be obvious if failed. It is my understanding that either would need to be removed to ID properly with a meter.
PAN-PCB components:
J1 – 8 pin click-mate connector
J2 – Micro HDMI port - 10118242-001RLF - https://www.mouser.com/ProductDetail/649-10118242-001RLF
J3 – Data/Power FFC - SFV14R-3STBE1HLF - https://www.mouser.com/ProductDetail/649-SFV14R-3STBE1HLF
J4 – HDMI FFC - FH55-22S-0.5SH - https://www.mouser.com/ProductDetail/798-FH55-22S-0.5SH
J5 – 3 pin motor wire connector
U1(2) – TI DRV8313PWPR - https://www.mouser.com/ProductDetail/595-DRV8313PWPR
U2 – TI TMS320F28067PNT - https://www.mouser.com/ProductDetail/Texas-Instruments/TMS320F28067PNT?qs=/ha2pyFadugKKKzuuRZuEPqRCfVoM/RbJd3NpS%2bIDFktfSzBPyCe6Q==
U3(2) – AD8210 - https://www.mouser.com/_/?Keyword=AD8210YRZ
U4(2) – AD8210 - https://www.mouser.com/_/?Keyword=AD8210YRZ
U5(3) – TI VP232 - SN65HVD232DR - https://www.mouser.com/ProductDetail/595-SN65HVD232DR
U6(1) – VN750PS - https://www.mouser.com/_/?Keyword=VN750PS-E
U7(1) – QUxx - MCP809T-450I/TT - https://www.mouser.com/_/?Keyword=MCP809T-450I/TT
R39 Bournes 3382G-1-252 https://www.mouser.com/ProductDetail/Bourns/3382G-1-252G?qs=2YQutYEabddkWwolD8h/Wg== @Ribs
(1) gimbal’s power & protection circuit(s)
(2) board’s motor control circuit, these duplicate to the other two boards.
(3) CAN Transceiver
(_) I’ve got no clue…
Y1 - ABM3B-20.000MHZ - https://www.mouser.com/Search/Refine?Keyword=ABM3B-20.000MHZ
Sorry to be long winded, it’s what I do. And before anyone asks… I do not offer any repair service as a business. Hope this effort helps someone else. Thank you 3DR for making this fine gimbal, still the smoothest camera platform for its size. Long live Solo, one gimbal at a time.
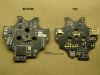
First, I am no electronics person and have no background for such things. I am a mechanical piddler, being that I fix and modify things that are mechanical. So I depend heavily on the knowledge of others, the internet and Mouser to plod my way through electronics’ issues. @just_bruce was my guide for trouble shooting this power faulted gimbal, Thank you Bruce.
If you find error with any of the following, please correct me. I’m just conveying my understanding for the component and its place within the given function.
The gimbal has three PCBs, each has CAN and a motor control circuitry for its associated motor. PAN, ROLL and TILT/Pitch. Here is what I understand for these three boards…
PAN-PCB – This board is typically the board to fail. It has the most exposure and the more delicate connectors. It distributes the various power and protection needs to the gimbal from Solo. Hosts the HDMI-FFC connection to the micro HDMI connector. And has a motor control circuitry.
ROLL-PCB – This board is strictly a motor control circuit board. It is somewhat vulnerable to damage or handling type failures. It taps off the power/data ribbon running down the gimbal. This board’s components allowed me to isolate the PAN-PCB’s power/protection circuit from the 8-Pin click-mate connector and then to the Data-FFC.
TILT-PCB – This is the main board of the gimbal, all the brains reside here. It is less likely to be the point of failure as it is well protected by its housing. The IMU, gimbal’s comms, Hero’s comms & port and a motor control circuit reside on this tiny board. It also has attached a potentiometer via ribbon cable to indicate its motor’s position.
HDMI’s ribbon is a homerun from the camera to the HDMI-FFC on the PAN-PCB. If you have video issues, isolated to the gimbal, then you basically have four items to inspect. Primary cause is the micro HDMI connector on the PAN-PCB. Then next would be the HDMI-FFC, ribbon or the HDMI micro that connects to the camera. There is no video conversion done on the gimbal, it all happens in the IMX6.
Data/Power ribbon, terminates to all three PCBs via its respective DATA-FFC, there are two version of this connector. If the ribbon is damaged in any way you are SOL, as there are no replacements unless by salvage. I can’t stress enough to release the ribbons from their FFC before disassembling a gimbal.
Final note regarding disassembly, all three motors have keyed shaft adapters held by grub screws to the keyed motor shafts. Orientation is critical, indicate/mark before disassembly. These adapters have through holes for securing to their respective arm, so orientation can be off by 180⁰ if improperly installed. Also the screw for the arm mount is secured by a grub screw through the end of the exposed adapter. Remove this grub screw first, it requires a 1.3mm hex.
So back to the original story, what I did to fix a dead gimbal. I tested the PAN-PCB board off the gimbal and powered by the J1 connector as normal from Solo.
I was able to isolate a protection/distribution circuit off the PAN-PCB. It appears that U6 & U7 make up that circuit. TP24 was reading about 2.940v, it should have the full battery voltage, 15.16v as an example. I believe the point of failure was between the two chips, not certain if both or one was faulted. I replaced U6 and the voltage tested low again at TP24.
Replacing U7 from a donor board and then TP24 showed the 15.16v. TP21 & TP22 prior was 3.48v and after U7 it was 4.26v. TP23 was zero on all tests, I assume this is the third phase of the BL motor.
I reassembled the repaired PAN-PCB to the gimbal and installed onto Solo. Initially the gimbal powered up with a green LED and then it turned orange indicating a reset or calibration. Once done it returned to green and I had full auto and manual control of the gimbal. It was stable in both low and high torque modes…success.
Here are the list of components that I’ve ID’d over the last few years. I have little ability to ID the traces through the boards, identifying what is what. Would be nice to have a schematic! Again trial and error, voltage and a continuity meter to hack through it all. As to resistors and capacitor, those will likely be obvious if failed. It is my understanding that either would need to be removed to ID properly with a meter.
PAN-PCB components:
J1 – 8 pin click-mate connector
J2 – Micro HDMI port - 10118242-001RLF - https://www.mouser.com/ProductDetail/649-10118242-001RLF
J3 – Data/Power FFC - SFV14R-3STBE1HLF - https://www.mouser.com/ProductDetail/649-SFV14R-3STBE1HLF
J4 – HDMI FFC - FH55-22S-0.5SH - https://www.mouser.com/ProductDetail/798-FH55-22S-0.5SH
J5 – 3 pin motor wire connector
U1(2) – TI DRV8313PWPR - https://www.mouser.com/ProductDetail/595-DRV8313PWPR
U2 – TI TMS320F28067PNT - https://www.mouser.com/ProductDetail/Texas-Instruments/TMS320F28067PNT?qs=/ha2pyFadugKKKzuuRZuEPqRCfVoM/RbJd3NpS%2bIDFktfSzBPyCe6Q==
U3(2) – AD8210 - https://www.mouser.com/_/?Keyword=AD8210YRZ
U4(2) – AD8210 - https://www.mouser.com/_/?Keyword=AD8210YRZ
U5(3) – TI VP232 - SN65HVD232DR - https://www.mouser.com/ProductDetail/595-SN65HVD232DR
U6(1) – VN750PS - https://www.mouser.com/_/?Keyword=VN750PS-E
U7(1) – QUxx - MCP809T-450I/TT - https://www.mouser.com/_/?Keyword=MCP809T-450I/TT
R39 Bournes 3382G-1-252 https://www.mouser.com/ProductDetail/Bourns/3382G-1-252G?qs=2YQutYEabddkWwolD8h/Wg== @Ribs
(1) gimbal’s power & protection circuit(s)
(2) board’s motor control circuit, these duplicate to the other two boards.
(3) CAN Transceiver
(_) I’ve got no clue…
Y1 - ABM3B-20.000MHZ - https://www.mouser.com/Search/Refine?Keyword=ABM3B-20.000MHZ
Sorry to be long winded, it’s what I do. And before anyone asks… I do not offer any repair service as a business. Hope this effort helps someone else. Thank you 3DR for making this fine gimbal, still the smoothest camera platform for its size. Long live Solo, one gimbal at a time.
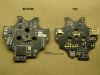
Last edited: