I believe I have a motor that is out of balance by a large margin. However after recording with my phone's accelerometer and a vibration app I'm not sure how to analyze the information correctly.
The motor testing was done one at a time through Mission Planner. The phone was placed on the battery laying flat on its back, with the top of the phone pointed to the front of the Solo.
Settings in MP - 50% Throttle for 2 seconds
App's Data sample rate was at 10ms intervals
I've charted 350 data points for each of the 4 motors, shown below.
I understand the magnitude of vibration is what I'm looking to solve. I'm not sure I set the test up correctly, but with everything the same it does offer some comparison data to work from. Is the relevant data the X, Y or Z when balancing a motor?
And then the other question is the frequency. The charted data shows different frequency for the vibration recorded. For example Motor 1's vibration frequency was short, whereas Motor 4's frequency was long. How does that figure into whether a motor is unbalanced or not?
Motor 4 is my questionable motor. Having recorded the data, it appears that 2 & 4 are similar.
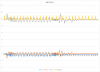
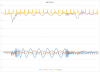
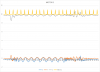
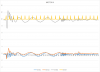
The motor testing was done one at a time through Mission Planner. The phone was placed on the battery laying flat on its back, with the top of the phone pointed to the front of the Solo.
Settings in MP - 50% Throttle for 2 seconds
App's Data sample rate was at 10ms intervals
I've charted 350 data points for each of the 4 motors, shown below.
I understand the magnitude of vibration is what I'm looking to solve. I'm not sure I set the test up correctly, but with everything the same it does offer some comparison data to work from. Is the relevant data the X, Y or Z when balancing a motor?
And then the other question is the frequency. The charted data shows different frequency for the vibration recorded. For example Motor 1's vibration frequency was short, whereas Motor 4's frequency was long. How does that figure into whether a motor is unbalanced or not?
Motor 4 is my questionable motor. Having recorded the data, it appears that 2 & 4 are similar.
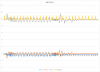
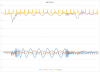
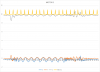
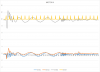